Nowadays, the busway or busduct is becoming widely know. The device is working as a power cable. To conduct an electricity (electrical energy) to the loads in different locations in an electrical system. Busway or busduct from most of the manufacturers are available in the range from 20-6,000 amp.
The following are their advantages electrical cable.
-
Require less space and installation time comparing to the cable
-
Lower total impedance than cable which resulting in less power loss and higher energy saving
-
Lower voltage drop than cable (at the same rated current)
-
Stronger and more durable than the cable
-
More suitable for variable load for example : convention center which requires frequent product line changing. Since the busway is more flexible to be tapped off to the load more than cable.
In order to understand busway better, we will discuss about its components:
Busway structures
Main components of the busway are (Fig 1) :
-
Conducter
-
Insulation
-
Housing
-
Ground System
-
Conductor : The Conductor is part that delivers electricity or electrical energy inside the busway. Copper or aluminum are usually used as conductor in the busway. Both metals have their own advantages and disadvantages for example, copper has better conductivity than aluminum but it is heavier while aluminum is lighter but it can have aluminum oxide at the poor plated contact which will be obstacle to the current transfer and can cause overheating at the contact. However, leading busway manufacturer such as Schneider Electric (Square D) has developed the Bi-metal technology in order to correct this problem.
-
Insulation : The insulation is the part that protects the contact between busway conductors. There are several insulation used in current busway such as PVC, Mylar, Epoxy, Polypropylene or Resin each type of these insulations have different advantages and disadvantage.
According to IEC 60439-2 standard which is the standard used as a reference in busway testing and it a widely accepted standard in Thailand, there is no identification or recommendation about the insulation which is more suitable for busway. The standard usually recommends the test according to requirements if the busway can pass the test, it will be assumed to be save and suitable for the application. The manufacturer will send the busway to certified test center such as ASTA of KEMA. The manufacturer will send the prototype to the test center and receive the certificate specifically for that prototype. This type of test is called 'Type test'. However, since it is frequently asked by user about the confidence that the prototype and the products available in the market will have the same performance and was produced under the same process and the same quality control system. The test center will have the other type of certificate to the test which is not only the sample part buy also the manufacturing. Processes to make sure that the product will have the same characteristics as the test specimens. The example of these certificates are UL Listed, ASTA Diamond or KEMA-KEUR (Fig 2). It is very expensive for the manufacturer to get these certificates and the manufacturer needs to have a high standard manufacturing process and quality control. There are few manufacturers who achieve this type of certificates. If the user would like to know the certificate that the each model of the products obtained, they can access to the following test center's websites:
http://www.kema.com/products_and_processes/Certified_products/Search_by_product_type/search.asp#O
http://database.ul.com/cgi-bin/XYV/cgifind.new/LISEXT/1FRAME/srchres.html
Mylar is one the material that many busway manufacturers use as insulation continuously (more than 40 years). It is accepted and proved as a proper material and technology for busway and has no problem on site. Supplier and manufacturer have mantioned about Mylar as follows:
2.1 What is Mylar?
Mylar is a type of polyester film made from polyethylene terepthalate. It has a polymer structure. Mylar has dielectric strength about 7,000 VoH. (at 1 mil thickness) and 23,000 psi tensile strength with and excellent corrosive resistant to chemical agents and humidity endurance. Mylay can also maintain its flexibility under the temperature ranging from -60oC to 150oC without any brittle characteristic throughout its life cycle.
2.2 Mylar reliability
Mylar was proved to be one of the best insulation material with the highest reliability. It was used as insulation in many devices not only busway but also electrical motor and transformer. Electrical motor manufacturers use Mylar as insulator for more than 40 years. In busway application, Schneider Electric, one of the leading busway manufacturer uses Mylar as insulation in model and l-Line II busway more than 40 years. The Mylar insulation in l-Line II busway by Schneider Electric has 7.5 mil thickness. This insulation is wound around the conductors two times. Other components wound by Mylar will always be tested with hi-potential test at 7,000 VDC (4,950 Vac, which is 8 times higher than actual application before) before assembly and deliver to the customers.
2.3 Mylar Electrical Characteristics
-
Dielectric Strength : Mylar with the thickness of 7.5 mil will have Dielectric strength about 2.7 kV/mil according to the test under short term dielectric strength standard (ASTM D-149) This dielectric strength of Mylar will decrease as the thickness increases as same as other materials.
-
Insulation resistance : Mylar has another interesting characteristic : It has a high insulation property even the temperature is increasing. Fig. 3 shows that its Dielectric strength of Mylar is nearly constant from 25oC to 150oC (higher than busway working temperature).
-
Humidity : Relative humidity has very low effect on Mylar's Dielectric strength Fig. 4 Dielectric strength varies less than +/- 10% form normal while relative humidity changes within the range of 20% - 80%
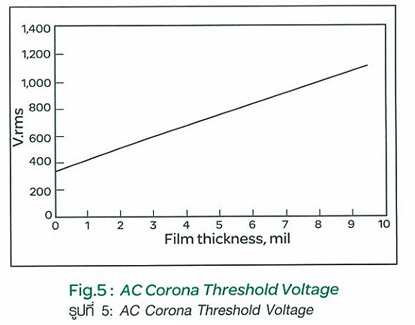
d. Corona Threshold Voltage : AC Corona which caused the corrosion of the material has no effect on Mylar polyester film if the alternated voltage is lower than the corona threshold in Fig. 5. Because Mylar has the highest corona resistance in plastic film. It can endure the corona all the way along the short surge range of the overvoltage.
e. Arc Resistance : From an arc resistance test (ASTM D495). It shows that Mylar has a good arc resistant. The timing test after the arc by observing the noise after the arc disappears from the surface to the material has shown that Mylar's arc resistance time is 73 to 94 seconds.
2.4 Physical and Thermal Property
Shear strength : shear strength was measured refers to ASTM D-732 standard. Mylar with the thickness 5 mil and 10 mil has 15 and 13.6 kg/mm2 shear strength respectively which is higher than other polymeric insulation.
Heat aging and Service lift : An information from Mylar manufacturer link DuPont recommends service temperature of Mylar about 150oC while its life cycle will decrease under the following working condition (1) under the condition that the Mylar plate was mounted incorrectly for example : warping of the plate (2) Application in dangerous condition or very dirty environment
(3) Application that the Mylar is exposed to other devices. The applications of Mylar in l-Line II busway will not have such conditions and will not affect to Mylay life cycle.
2.5 Chemical Properties
Mylar film Chemical properties test reveals its excellent resistance to chemical reagent, solvent, different kind of Varnish and contaminants, Moreover, Mylar has an impermeable property. The test has shown that oil and grease cannot pass through a 1 mil thick Mylar film enen it was left in a room temperature for 2 months. The test according to ASTM D-570-63 standard found that Mylar will absorb the moisture less than 0.8% when put into the water for 24 hours.
Mylar manufacturing processes according to the information from DuPont (Mylar manufacturer from US. that was selected by Schneider Electric, the leading busway manufacturer, to use their Mylay as busway insulation) shows that there are 5 main processes : Polymer preparation, Casting, the Draws, Crystallization and Roll formation.
Process 1 Polymer Preparation
The raw material in Mylar manufacturing is called Polyethylene terephthalate (PET) prepared from PET chip will be dried up and passed to extruder with a large screw in the pipe extruder will be heated. The heat and pressure from the screw will melt the polymer. Then the melting polymer will be sent to the filter in order to discard contamination.
Process 2 Casting
This process is the actual beginning of the film manufacturing process. The melting polymer will flow through an automatic controlled slot, the melting polymer will go into a large casting drum. This casting drum is rotating slowly and its inside is cooled by a cooling water. The cool film that has passed through the melthing process will have thickness about 2 mm. And the molecular structure will change to amorphous.
Process 3 The Draws
The film will be slowly drawn through rollers from casting drum to forward draw of the draw process. Then, it will go to the heating zone in a short interval to heat the upper and lower side of the film to about 90oC until the film is soft enough to be drawn. The heated film will be sent to the roller which will accelerate the speed to 3 times This acceleration will increase the film length to 3 times and some of the molecules will be rearranged into the moving direction. After that the film will be sent to sideways draw or stenter. In the stenter, the film will be heated to 100oC and when the rail move backward the film length will be 3 times of the starting length. At this point, we will have a polyester film with a proper thickness which is 10 times thinner from the starting thickness. There are 3 arrangements : aligning with the moving direction from forward draw, aligning in a counter direction to the moving direction from the Sideways draw and the arrangement which is amorphous.
Process 4 Crystallization
After the draw, the film will have a low flexibility. The crystallization will increase its by arranging as crystal because the PET crystal is stronger than an amorphous. Making some area of the film to be crystal will make the film stronger. After the final step of the draws, the film temperature will be about 200oC which is high enough to make the molecule arrangement to be crystal.
Process 5 Roll Formation
In this process, the film will be cut into strips or wound up to rolls according to the size required by the customer and the film will be tested before deliver to the customer.
All this processes are controlled by automatic machine and the quality checked will be done by Dupont engineer in each step. DuPont is known is a strict company which has an attitude that the quality is the organization's culture.
2.6 Recycle Properties & Green technology
One of best properties of busway used Mylar as insulation is that it's easily recycled when end of service life. It's one of Mylar advantage over other insulation which is required a complicate recycle technology.
Summary
The busway has the following main components : conductor, insulation, housing and ground in order that the user can use the busway safety, standards are used to establish the requirements, for example , IEC60439-2 which is the standard that the busway manufacturer should pass and certified. The certification can be done by the manufacturer by doing the type test which is sdending the speciment to test or spending more to test and check the manufacturing process (KEMA KEUR, ASTA Diamond or UL listed) so that the user will be ensured that the products will have the same quality as the specimen.
References :
1. Bulletin No.5600PD9601, Mylar Busbar insulation-A thirty year trackrecord, page 1-4, July 1996
2. Information note 16 Issue2, Product information 'Melinex and Mylar polyester film-how they are made and how DuPont tailors them to your needs, DupontTM, page 1-6,
3. Mylar polyester film Safety in hadling and use, DupontTM, page 2
4. Mylar polyester film Electrical Properties, DupontTM, page 1-8
5. Spectra Series Busway, GE consumer & Inductrial Electrical distributioncatalog, page 7, 2007
|